Подшипники для электродвигателей
Типы подшипников
Подшипники служат опорами вала в электродвигателе.
Подшипники разделяются на 2 типа:
- подшипники качения;
- подшипники скольжения;
В зависимости от формы тел качения, подшипники качения бывают:
- шариковыми;
- роликовыми;
- игольчатыми;
Подшипники скольжения и игольчатые подшипники
Подшипники скольжения и игольчатые подшипники используются в электродвигателях бытовых электроприборов. Они, как правило, применяются для систем с обдувом (например, в вентиляторах), когда необходимо обеспечить низкий уровень шума.
Шарикоподшипники
Шарикоподшипники используются практически во всех типоразмерах электродвигателей для промышленного применения, включая электродвигатели насосов. Шарикоподшипники имеют следующие преимущества:
- работают в широком диапазоне температур;
- подходят для работы с высокой частотой вращения;
- обеспечивают небольшие потери на трение.
Выделяют несколько типов подшипников: открытые шарикоподшипники, шарикоподшипники с одной защитной шайбой и уплотнённые шарикоподшипники.
Роликовые подшипники
Большинство роликовых подшипников состоит из трёх компонентов: колец с дорожками качения (внутреннее кольцо и наружное кольцо), элементов качения (шариков или роликов) и сепаратора для элемента качения. Сепаратор подшипника имеет несколько функций, например, он разделяет элементы качения, удерживает их между внутренним и наружным кольцами так, чтобы элементы качения не выпадали и при этом свободно вращались.
Выделяют два типа элементов качения: шарики и ролики. Контакт шарика и дорожки осуществляется в точке, а ролика — по линии. Ролики бывают четырёх типов:
- игольчатые
- конические
- цилиндрические
- сферические
На элементы качения и кольца подшипников приходится вся нагрузка, приложенная к подшипнику.
Маркировка/кодовое обозначение подшипников
Маркировка подшипников представляет собой кодовую комбинацию, которая отражает такие показатели, как размер, модель, конструкцию, точность и т.п. Она включает в себя несколько букв, которые формируют три базовые группы кодов: основной цифровой код и два дополнительных кода. Основной цифровой код содержит общую информацию о модели подшипника, габаритные размеры и др., а также информацию о коде угла контакта, о номере диаметра расточенного отверстия и последовательном коде подшипника.
Два дополнительных кода выводятся из серии префиксных кодов и серии конечных кодов. Эти коды представляют информацию о внутреннем зазоре, погрешности подшипника и целый ряд других показателей, которые относятся к внутренней конструкции и спецификации подшипников.
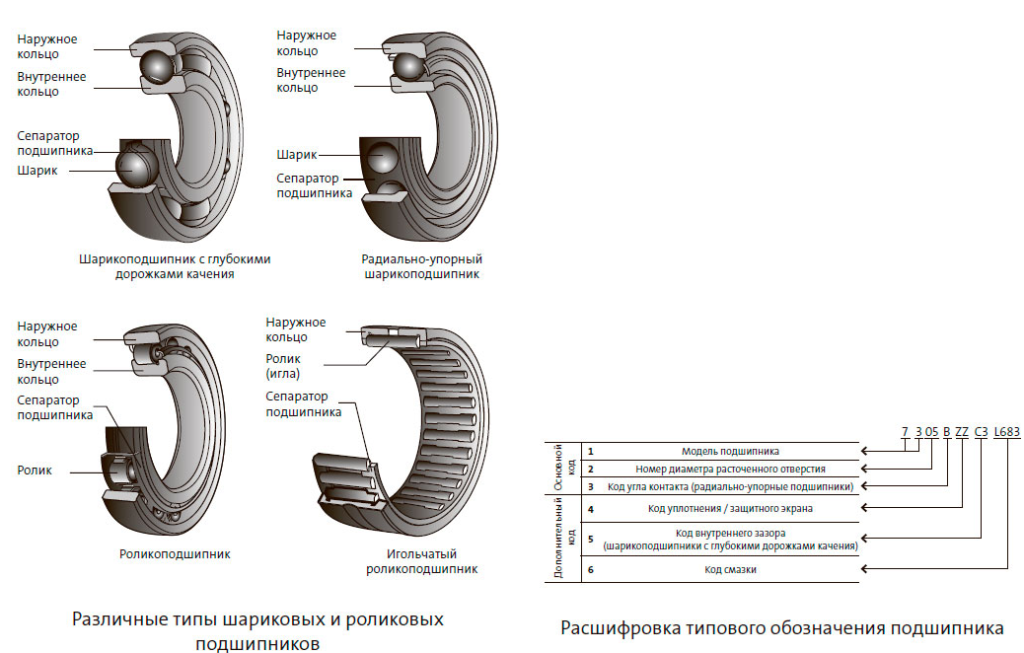
Габаритные размеры
Электродвигатели оснащены высококачественными подшипниками следующих производителей:
- SKF
- NSK
- NTN
- FAG (INA)
Типоразмеры подшипников стандартизированы. Сведения приведены в ISO 15 и ISO 492.
Зазор в подшипниках
Принцип работы подшипников качения таков, что одно из колец (наружное или внутреннее) всегда остаётся подвижным, даже если другое зафиксировано. Зазор представляет собой допустимое перемещение для кольца. Выделяют два вида зазоров: радиальный внутренний зазор и осевой внутренний зазор.
Радиальное допустимое перемещение кольца является радиальным внутренним зазором, а осевое допустимое перемещение — осевым внутренним зазором. Как правило, осевой внутренний зазор в 6-10 раз больше радиального внутреннего зазора.
Американская ассоциация производителей подшипников (ABMA) и ISO представили классификацию радиальных внутренних зазоров для подшипников. Выделяют пять классов зазоров:
- C2
- CN, стандартный зазор
- C3
- C4
- C5
C2 является наименьшим допустимым зазором, а C5 — наибольшим, по отношению к внутреннему диаметру подшипника.
Радиальный внутренний зазор — это промежуток между верхним шариком и наружным кольцом.
Выбор внутреннего зазора подшипника
Первоначальный внутренний зазор — это значение зазора, с которым подшипник выпускается при производстве. Рабочий внутренний зазор — это зазор, характерный для подшипника при его монтаже и эксплуатации. Для того чтобы увеличить ресурс (долговечность) подшипника, теоретически он должен иметь по возможности минимальную величину внутреннего зазора при нормальной рабочей температуре.
Однако поддерживать оптимальные значения зазора в нормальных рабочих условиях трудно. Меняющиеся рабочие условия могут привести к тому, что зазор уменьшится настолько, что вызовет перегрев подшипника, в результате чего сократится его ресурс.
Когда шарикоподшипники с глубокими дорожками качения нагружены в осевом направлении, целесообразно увеличивать рабочий зазор.
Очень важно выбрать рабочий внутренний зазор, значение которого будет минимальным.
В нормальных условиях эксплуатации (т.е. при нормальной нагрузке, посадке, частоте вращения и температуре) величина рабочего зазора, равная CN, является удовлетворительной с точки зрения долговечности подшипника.
Выбор первоначального зазора
Первоначальный зазор — это фактическая величина зазора подшипника перед установкой, он обозначается, например, как: C3 или C4. Рабочий зазор — это фактическая величина зазора после установки подшипника и во время эксплуатации, когда на него влияет перепад температур. Рабочий зазор влияет на подшипник во время эксплуатации, а именно на уровень производимого шума, вызывает усталостную нагрузку подшипника и его нагрев.
Ресурс подшипника может быть большим, если зазор будет минимальным. Но если величина рабочего зазора будет ниже определённого уровня, ресурс подшипника будет очень маленьким. В связи с этим величина первоначального зазора должна быть такой, чтобы значение рабочего зазора было положительным.
Кроме зазора необходимо учитывать монтажные размеры, от которых зависит возникновение посадки с натягом между подшипником и валом. Кроме того, очень важно учитывать разность температур между внутренним кольцом и наружным. Как правило, разность температур составляет 10 — 15 K, так как потери в роторе электродвигателя преобразуются в тепло, которое выводится через вал и подшипник.
Благодаря плотной посадке и разности температур подшипники с зазором C3 обычно используются в электродвигателях переменного тока.
Подшипники с зазором C4 часто используются в электродвигателях насосов как DE-подшипники (подшипники со стороны привода). Это объясняется тем, что подшипник с зазором C4 может воспринимать большие осевые нагрузки, чем подшипник с зазором C3. Поэтому ресурс подшипников с зазором C4 больше в тех областях применения, где прилагаются, в основном, осевые нагрузки,— например, в небольших многоступенчатых насосах.
Очень важно при замене подшипника устанавливать новый подшипник с зазором такого же класса. Если электродвигатель оборудован подшипниками C3, а новые подшипники имеют зазор C4, появляется риск возникновения шума.
Если электродвигатель оборудован подшипниками C4, а новые подшипники имеют зазор C3, может уменьшиться ресурс подшипников. Такая замена не рекомендуется.
Этапы демонтажа
Перед тем, как заменить подшипники электродвигателя, нужно их снять. Чтобы провести эту операцию вам нужны съемники. Важно учитывать, что они отличаются по размерам и с точки зрения конструкции, поэтому, если не уверены, возьмите в магазин двигатель, чтобы подобрать подходящий съемник.
В принципе, можно прикинуть, и купить съемник «на глаз»:
- Для маленьких валов подойдет механизм со съемными планками захвата.
- Для вала побольше стоит брать массивный съемник с 3-4 лапами, захватывающими подшипник.
Если вы работаете съемником, придется приложить усилия, чтобы вращать его. Если слишком тяжело, возьмите кусок трубы, чтобы удлинить рычаг. Для более легкого снятия можно смазать вал машинным маслом или смазкой WD-40.
Как установить новый подшипник
Насаживать подшипники на ротор можно разными способами, а именно:
- С применением усилий. Берут металлическую трубу, такую, чтобы диаметры её и подшипника совпадали. Забивают деталь на место, ударяя самой трубой или небольшой кувалдой по трубе.
- С предварительным нагревом. При нагреве деталь расширяется, и её можно поставить на месте без чрезмерных усилий.
Удобно нагревать подшипник, поместим его в кипящую жидкость, например, в масло. Главное — извлекать осторожно, иначе можно обжечься при извлечении горячей детали.
Установив детали на свои места, пространство заполняют смазкой на две трети. Часть пространства оставляют незаполненной. Выполняют сборку этой стороны двигателя, затем весь процесс повторяют с другой стороны в аналогичной последовательности.
Выбирая качественные комплектующие и соблюдая аккуратность при демонтаже и установке подшипников, можно приблизить срок эксплуатации электродвигателя к максимальному.
Эксплуатационная необходимость в смазках
Подшипники применяются в электродвигателях в качестве опоры ротора и обеспечивают равномерность его осевого вращения и недостаточное количество смазки, равно как ее низкое качество, обуславливает снижение скользящего эффекта и провоцируют конструктивное намагничивание колец подшипника, а при обильном количестве она может попасть в электрическую машину и спровоцировать ее выход из строя.
Соответственно, замена смазки в подшипниковых узлах должна быть регулярной и своевременной, так как высокие температуры, вызванные значительными нагрузками и скоростями, продукты коррозии и механические взвеси приводят к ее окислению и утрате ею изначальных характеристик. Но при этом не следует забывать, что каждая замена смазки в подшипнике или втулке сопряжена с выводом электродвигателя из эксплуатации, что обуславливает простои и повышенные материальные затраты.
Применение специальных высокотемпературных и высокоскоростных смазок для подшипников – лучшее инженерное решение, которое позволяет:
- Увеличить межсмазочный интервал.
- Оптимизировать расходы на эксплуатацию и ремонт путем качественного смазывания подшипников.
- Обеспечить высокую производительность и стабильную работу электрического оборудования.
- Выйти на требуемую скорость вращения
Эксплуатационные свойства и применение смазочных материалов для подшипников
Назначение смазки, закладываемой вручную или подаваемой в подшипники механизированным способом, заключается в следующем:
- Минимизация внутреннего трения подшипниками скольжения.
- Герметизация подшипника от попадания механических частиц, пыли, окалины.
- Отвод тепловой энергии, которая образуется в результате трения, значительных внутренних напряжений и передается от нагретого вала двигателя, эту функцию выполняют смазочные масла входящие в состав смазки.
- Защита металлических конструктивных элементов от коррозии.
- Уменьшение вибраций и шумов.
- Увеличение срока службы подшипников работающих в тяжелых условиях работы
Виды применяемых смазочных материалов
Теоретически, как часть электрооборудования, подшипники могут обрабатываться густыми и жидкими смазками, но из-за вероятности попадания в обмотку на практике масла практически не применяются. Зато консистентные смазки с расширенным температурным диапазоном нашли широкое применение на всех видах электродвигателей. Они превосходно выдерживают значительные нагрузки, устойчиво противостоят выдавливанию смазочных материалов и воздействию центробежных сил. Поэтому очень важен выбор смазки, в нашем случае - пластичных смазок, от этого на 70% зависит долгая работа подшипника.
Для эффективного и долговременного смазывания при подборе следует учитывать:
- Конструктивные особенности подшипников качения и электродвигателей.
- Характер эксплуатации (скорость вращения, режим работы, весовые и мощностные нагрузки).
- Специфика среды эксплуатации (влажность, перепады и пределы температур, наличие химически агрессивных веществ и механических взвесей).
Таким образом, в зависимости от конкретики условий эксплуатации для обработки подшипников или втулок могут использоваться смазки:
- Высокоскоростные. Применяются в электродвигателях с повышенными параметрами частоты вращения или со стабильно изменяющейся скоростной нагрузкой. Должны иметь консистенцию класса NLGI 2 и достаточно высокую температуру каплепадения, обеспечивать отличное отведение тепла и обладать повышенными противозадирными свойствами. Чаще всего рекомендуется при чрезвычайно высоких скоростях использовать смазки на базе синтетических базовых масел.
- Высокотемпературные. Применяются консистентные смазочные материалы с высокой стабильностью и имеющие отличные антифрикционные свойства. Используются для подшипников, сопряженных с температурами окружающей среды выше + 120 ˚С.
Вязкость и скоростной режим
Ключевым параметром, который определяет эксплуатационные качества любого смазочного продукта, является вязкость базового масла. Важно помнить, что вязкость и консистенция — не одно и то же, эти параметры характеризуют разные свойства смазочного материала. На что влияет вязкость базового масла? В первую очередь, чрезмерно вязкая смазка отличается термической нестабильностью и, при повышении температурно-скоростного фактора, повышается трение скольжения. Это влечет за собой увеличение периодичности закладки смазки и сникает рентабельность производства. Для расчета скоростного фактора используется формула: Dn = N/2 * (Dнн + Dвн), где: N — частота вращения, об/мин, Dнн и Dвн — наружный и внутренний диаметр подшипника, мм Получив значение скоростного фактора, можно подобрать рекомендованный параметр вязкости базового масла. Для этого понадобится значение средней рабочей температуры. Следует отметить, что полученное значение актуально только для подшипников, эксплуатируемых с небольшими нагрузками. Если значение нагрузки повышенное или экстремальное, параметр необходимо увеличить в 2 и 3 раза соответственно. Также подходящее значение вязкости базового масла можно узнать из таблицы:
Особенности применения | Скорость | Вид подходящего смазочного материала | Уровень вязкости базового масла при температуре +40˚C |
Маленькая скорость | 50 000 | Общепромышленного назначения | 1 000 - 1 500 |
Невысокая скорость, но большое давление | 200 000 | Промышленного назначения для подшипников и узлов | 400 - 500 |
Высокая скорость и нагрузка | 600 000 | Многоцелового назначения | 100 - 220 |
Скорость выше средних показателей, температура высокая | 600 000 | Смазка пролонгрированного действия | не больше 70 |
Крайне высокая скорость | не меньше 1 000 000 | Смазка длительного действия | 15 -32 |
Каналообразование
Этот параметр очень важен при подборе смазки, он обозначает предел текучести и проникающую способность смазки. Для определения параметра проводят тестовые испытания. Методика испытания регламентируется Федеральным стандартом 791С-6.2. Согласно методу 3456.2, смазка наносится на тестовую поверхность равномерным слоем. Когда температурное воздействие стабилизируется, на смазанной поверхности создают тестовый канал, проводя по ней стальным калибровочным инструментом. Через 10 секунд проверяется степень заполнения канала и чем она больше, тем лучше обволакивающие свойства смазочного материала. По результатам испытаний все материалы относятся к одному из двух типов — обволакивающему или необволакивающему. Смазки первого типа глубже проникают в конструктивные пазы и создают тонкую, прочную пленочную поверхность, обладающую защитным и антифрикционным эффектом. Преимуществом обволакивающих смазок является быстрое удаление излишков, в результате чего стабилизируется теплоотвод и предотвращается пенообразование. Избытки смазок необволакивающего типа наоборот, затекают обратно и при повышении скорости могут пениться, провоцируя перегрев.
Тип загустителя
Загустители в смазочных материалах выполняют роль коллоидного уплотнителя, формируя структуру молекулярного каркаса и оказывая влияние на показатель каналообразования. Кроме этого, загустители стабилизируют текстуру, определяют свойства пенетрации, водостойкости, устойчивости к выдавливанию и влияют на предельные значения температуры каплепадения смазки. Качественный загуститель не должен вызывать коррозию или ухудшить смазывающие свойства материала. Загустители, содержащие кальций, кремний, литий и полимеры сложных эфиров, обладают гладкой равномерной текстурой. Такие загустители оптимизируют динамические свойства и улучшают каналообразующие характеристики смазочных материалов. Содержание алюминия, бария и натрия наоборот ухудшает каналообразующие характеристики, способствует вспениваю и сникает стабильность консистенции.